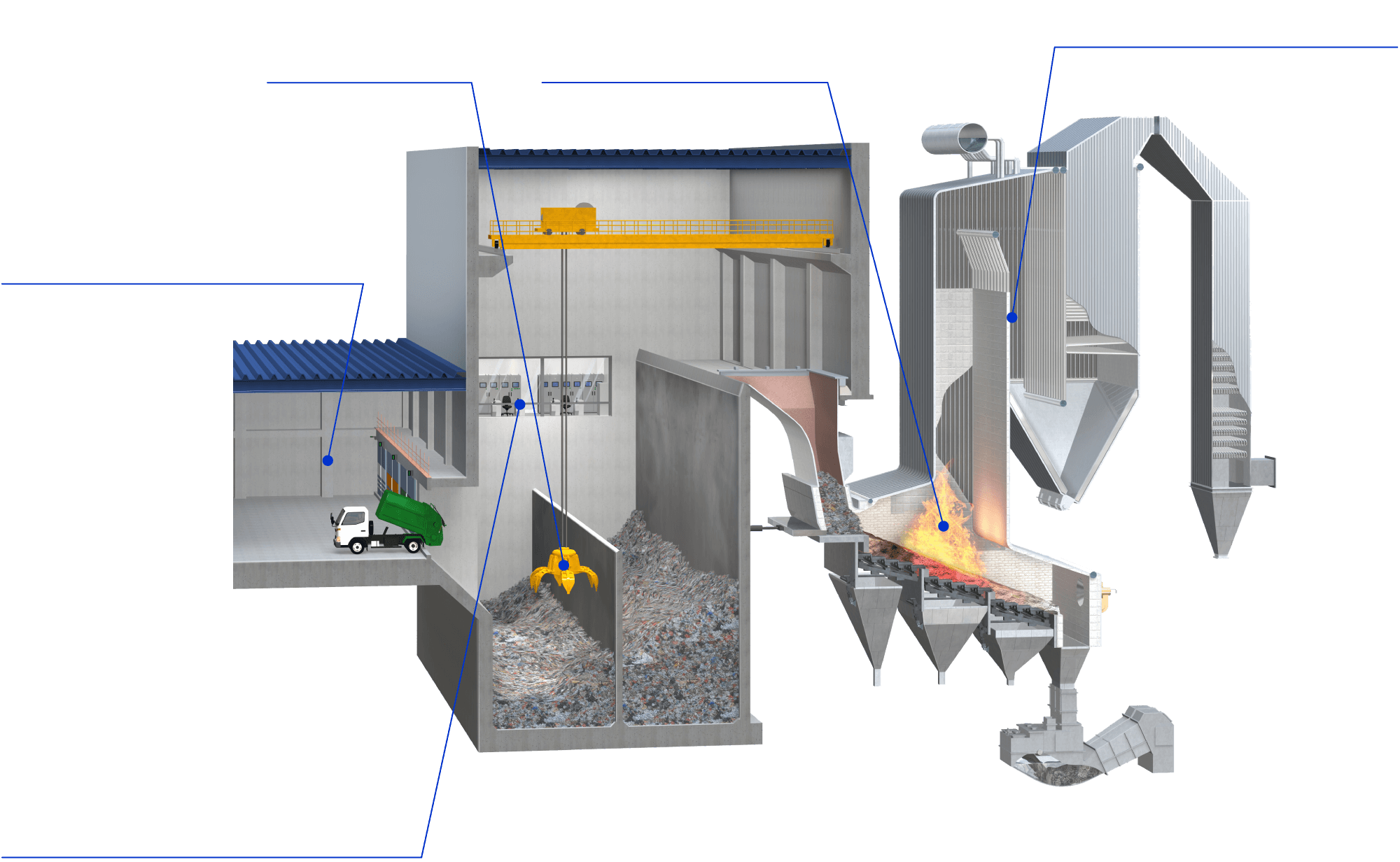
Specifically, we are incorporating state-of-the-art technologies like AI and ICT,
which are being developed at a dizzying pace, into our plants,
and we are developing new labor-saving and automation technologies for use at waste treatment facilities.
01
Trucks transporting waste are identified by a license plate scanner during the reception, eliminating the need to scan IC cards or fill out intake forms. Automatic guidance of trucks to unloading platforms and use of automatic fee adjustment machines at exits reduce labor requirements while boosting convenience.
02
Until now, automatic crane operation resulted in insufficient mixing to keep waste uniform, requiring an operator to visually monitor conditions in the pit and accomplish mixing by means of manual operation. We developed an image recognition system to reproduce this visual monitoring and improve mixing performance.
03
We developed the Intelligent Control System (ICS), an AI-based combustion control system, that predicts future combustion trends based on combustion imagery and operational data and operates the equipment as necessary in response. This system realizes stable combustion while reducing the amount of manual operation performed in the past by operators by 99%.
04
We have established technology for reducing overall manual operation at plants by 99% by augmenting our AI-based combustion control system with functionality for automatically adjusting boiler evaporation volume function and the amount of chemicals supplying function by flue gas treatment equipment.
05
Our Solution Lab, which provides functionality similar to a central control room for facilities and which is staffed 24 hours a day with experienced technicians, provides support for facility operations. In addition, remote control functionality keeps facilities operating in a stable manner with low staffing levels and unattended central control rooms.
06
POCSYS, Takuma’s proprietary operational support system, makes it possible to visualize operating conditions and equipment performance by facilitating the central management and analysis of facilities’ operational and maintenance data. We identify issues by evaluating facilities’ operational track record based on the results of such analysis, analyze their causes, and propose solutions.
07
We have developed a system for compiling operation plans that satisfy various constraints and requirements in facility operation using performance data accumulated by POCSYS and mathematical optimization techniques. We provide the best possible operational services at the lowest possible cost, for example by maximizing power sales and improving profitability.
08
We use an operational training simulator that reproduces plant operation in a virtual space during operator education and training in order to help trainees master a broad range of knowledge and skills related to facility operation. This approach also lets trainees learn operational procedures used in the event of emergencies, which typically cannot be experienced during actual operation.
Waste incinerator operators can slash manual operation by 99% by installing Takuma’s Intelligent Control System (ICS), an AI-based combustion control system. In addition, we have established technology that allows two operators to operate a facility in a safe and stable manner, which is a lower staffing requirement than in the past, thanks to remote monitoring and control from our Solution Lab.
Solution Lab provides remote monitoring and operational support by monitoring plant status and operating conditions 24 hours a day. It offers high-quality services that utilize the latest information and communications technologies (ICT) to provide optimized solutions for customers and support to help ensure safer, more secure plant operation.
POCSYS brings together plant operating and maintenance management data to provide real-time integrated management of plant and equipment operating status. By analyzing and evaluating accumulated data and providing feedback to operational personnel, we are able to improve the quality of plant operation while lowering life cycle costs.